1 Preface
"Green, environmentally friendly, and intelligent" has become the development direction of enterprises and industries in the new era. As a concrete mixing station, colleagues are also working hard to study along this direction to explore how this "mud-heavy" equipment can be used in the future. Development in the direction of “green, environmental protection, and intelligence”. After the country's "environmental protection storm", concrete mixing station manufacturers have successively launched "fully enclosed factory-style" mixing stations, which is also known as the "fifth generation green environmentally friendly concrete mixing station" by the industry. But when we look back, Can this fully enclosed mixing station be called a "green" mixing station? What is "green"? The cost of the entire package is higher than the mixing station itself, which requires a large amount of external packaging insulation and steel structure materials. It is better for commercial concrete mixing stations because the life cycle of the entire equipment is longer, at least ten years, but for engineering concrete mixing This is very bad for the station. The general project cycle is 3 to 5 years. The relocation of the equipment will inevitably cause a lot of waste due to the inability of the outer packaging to be used. Therefore, as a fifth-generation mixing station, it can only be said that it plays an important role in environmental protection. It cannot be called "green". Therefore, the "fifth generation" mixing station is only a measure taken at this stage to meet the national environmental protection requirements, not the "essential" environmental protection of the equipment, let alone "green". We should be committed to improving the "essence" of the mixing station to promote "Heniba" equipment is developing in the direction of "green, environmentally friendly and intelligent".
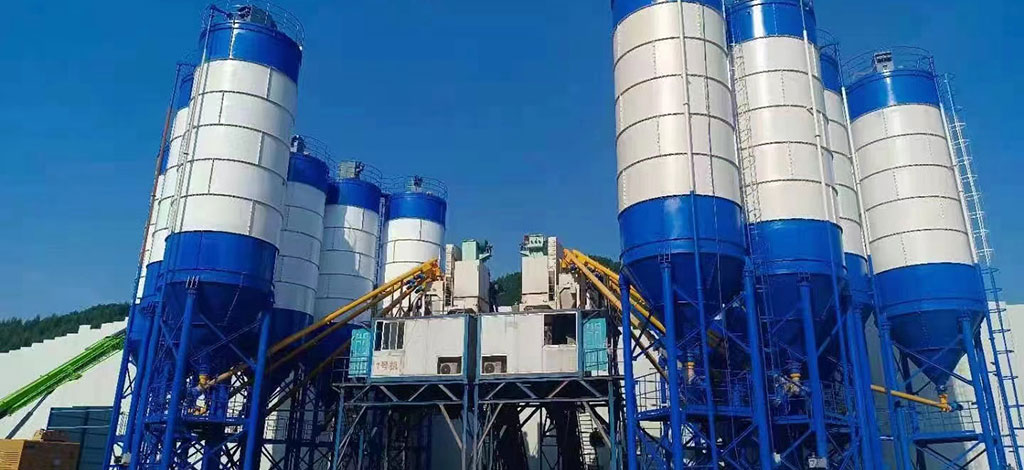
2 Understanding of Green Mixing Station
First, let’s talk about what “green engineering” is. In the field of engineering construction, it is defined as follows: creating more efficient technologies and processes through measurement and control technology to obtain environmentally friendly products and systems. NI provides measurement, automation, and design tools that collect and analyze real-world data and then debug or resolve any issues discovered by the user. The ultimate goal is to better benefit our planet through more efficient and cost-effective technologies. This is a complete definition of "green engineering" in the field of engineering construction. I think it is well described and is also applicable to "green mixing stations". Of course, the construction of the mixing station itself is also a part of engineering construction.
From the above definitions, we can conclude that there are some salient features of green mixing stations: economy, energy saving, and intelligence. Maximize resource utilization and reduce waste; save energy, reduce emissions, and reduce environmental pollution; equipment maintenance and operation are humane and intelligent, meeting the requirements of modern engineering construction.
Industry seniors have also proposed the overall development direction of "green and environmentally friendly mixing stations" with "one concept, five innovations, eight features, and four value-added services", which involves development concepts, technological innovation, performance indicators and upstream and downstream industrial chains. In terms of extension and other aspects, it is worthy of our efforts to promote the development of green mixing stations based on previous research, build the concrete mixing station into a model of "green engineering", and promote the green development of the concrete mixing industry.
3. Some understandings of the research direction of green concrete mixing stations
(1) The structure of the mixing station itself meets environmental protection requirements, reducing the need for users to use overall external sealing to solve problems such as emissions and noise, and reducing construction costs. Adopt modular design to solve the waste caused by equipment relocation, such as exterior decoration waste, foundation waste, transportation waste, etc. Now some technologies have been applied, such as foundation-free mixing station application, chip powder silo application, plug-in wiring, etc. Among them, the application of chip powder silos has particularly obvious economic and social benefits, and is gradually recognized by users. Originally, especially in engineering construction projects, equipment relocation caused a large number of powder silo disposal problems, resulting in a lot of waste.
At present, the environmentally friendly outer packaging of the main building of the mixing station is mainly to solve the problem of dust spillage from the main building, including dust from the main building and dust from the powder silo. Dust from the powder silo is the main factor. In the past, factors such as inaccurate material level in the silo and blockage of the dust collector were caused. The "explosion" phenomenon has caused serious pollution, but now these problems can be said to have been well solved from a technical perspective, such as weighing level sensors, smoke sensors and other applications. This is also the advancement of the application of sensing technology to be mentioned later. The problem of "intelligentization" of concrete mixing stations. Therefore, the improvement of the intrinsic environmental protection performance of the mixing station promotes the transformation from "dust spill-proof outer packaging" to "decorative outer packaging" to reduce the construction cost of the main building.
Regarding the storage of aggregate silos, most currently use greenhouse-type structures to reduce dust spillage and noise problems (mainly from loader loading). Commercial concrete mixing stations are gradually developing towards the use of three-dimensional silos. Is it also possible for engineering stations? Promotion is worthy of study, which must consider issues such as aggregate transportation distance, concrete production capacity, and the relocation and utilization of steel structure silos.
In short, reducing the construction cost of concrete mixing stations should be one of the problems solved by the "sixth generation green mixing station".
(2) In terms of energy saving, the mixing station itself mainly includes three aspects: the reasonable allocation of power of each component, efficient control system and efficient mixing system. It boils down to one indicator: the energy efficiency of the mixing station, that is, the mixing station produces per cubic meter of concrete. energy consumption.
Whether it is the national standard or the previously formulated group standard "Energy Efficiency Testing and Evaluation Methods for Concrete Mixing Stations", although some evaluation indicators are given, I personally think that there is a lack of data support and systematic data collection and analysis. At the same time, although users sometimes emphasize energy saving However, the specific problem is still extensive. For example, based on reasonable calculations and actual data testing, the power can be reduced, but users think that low power means reduced reliability. In any case, as an industry development, improving the energy efficiency of mixing stations is our research direction. Among the eight characteristics of the "green and environmentally friendly mixing station" mentioned earlier, experts also proposed "low energy consumption, high efficiency" and specific indicators, such as reducing energy consumption by 25%, increasing production efficiency by more than 20%, etc. Of course, these two aspects are also related.
Research on high-energy-efficiency mixing stations should be carried out from different working conditions, such as what we usually call engineering stations, commercial mixing stations, pipe pile stations, PC stations, etc. Since concrete performance requirements are different in different working conditions, such as high-speed rail concrete mixing time standard requirements 120s, pipe piles and PC stations require 60-90s, and ordinary commercial mixing only requires 30-40s. In this case, if an ordinary mixing host is used, the power of the supporting components needs to be reasonably configured to reduce the overall equipment energy consumption. For example, the spiral supporting equipment of a high-speed railway station is one specification lower than that of a commercial mixing station, which not only reduces energy consumption, but also reduces costs; The inclined belt conveyor should also have some energy-saving configurations. For commercial mixing stations, we should focus on researching high-efficiency mixing hosts and efficient control systems to improve the energy efficiency of the mixing stations. For example, according to the 4-party host, the mixing time of the ordinary mixing host cannot be less than 45 seconds, and the mixing time control of the high-efficiency mixing host It can be done in 30 seconds, thereby achieving the goal of increasing production efficiency by 20%.
Reasonable configuration for different working conditions does not mean a reduction in product standardization, but is the research and development direction of "green mixing stations". In particular, companies leading the development of the industry must make great efforts to research and promote energy-saving concrete mixing stations. Regarding the "minimum mixing time should not be less than 2 minutes" stipulated in the "6.6.5" clause of the "Technical Guidelines for Railway Concrete Engineering Construction" No. 241 of China Railway Construction [2010], the association should work with the Academy of Railway Sciences to promote the use of mixing hosts in colleges and universities. application, shorten the mixing time and improve the energy efficiency of the equipment. Due to the relatively long mixing time of the high-speed railway mixing station, the 3-cubic-meter station is less than 60 cubic meters per hour. If the calculation is shortened by 30 seconds, the economic and social benefits created will be considerable. In the early stage of this work, experts from the China Railway Institute’s materials research were also committed to promoting it, but there has been no result so far. In response to this problem, we actually put forward a new development idea for us as a manufacturer of concrete mixing stations, that is, we must strengthen cooperation with upstream and downstream Jointly engage in scientific research and strengthen technical exchanges. Take the high-speed railway mixing station as an example, which requires mixing for 120 seconds. As a manufacturer of mixing stations, some say it is for the powder material to better coat the aggregate surface; some say it is to reshape the aggregate and use better concrete pouring. Improve the performance of concrete; some say it is to ensure that the additives are mixed evenly, etc. Assuming that these problems exist, do manufacturers of concrete mixing stations also have solutions to reduce mixing time?
(3) In terms of intelligence, it mainly includes three aspects: the application of sensing technology, the application of "5G" network technology, and the upgrade of intelligent software control systems. These three aspects are also complementary and interlocking, and ultimately form a The intelligent operation control platform integrates monitoring, diagnosis, and control through signal conversion and transmission, and performs IoT project management. It is a higher stage of the "green mixing station" and is also the inevitable development direction. The application of sensing technology is the hardware foundation for the intelligentization of mixing stations. From the perspective of the sensor technology itself, it is already quite mature and has mature applications in high-precision and professional industries. Here is an example of the main sensor applications of current mixing stations: powder The system includes feeding control detection, weighing material level detection, warehouse pressure detection, smoke detection, etc. It is explained here that the warehouse pressure detection does not refer to the pressure safety valve, and the pressure safety valve is not an environmentally friendly equipment; belt material flow detection, belt speed detection , deviation detection; aggregate temperature detection, moisture content detection, material level detection; main engine oil level detection, oil temperature detection, shaft end seal detection, concrete moisture content detection; door opening and closing detection of each material port; each weighing scale Weighing sensor detection and so on. The intelligent software control system should mainly include functional modules such as intelligent calculation, logical interlocking, multiple judgments, self-fault diagnosis and repair. Let me explain here that the ERP management system of the mixing station cannot be called intelligent, it can only be said to be intelligent. An intelligent database can only be intelligent if it uses an intelligent software system to realize the functions of each module. For example, the management of cement consumption is a very important material management module of the mixing station. Only data such as loading weighing detection, production measurement detection, and concrete volume produced are intelligently calculated to form a management judgment data and provide cement consumption deviation alarms. .
It can be said that there is no clear standard in terms of intelligence, and in fact it is impossible to have a unified standard. We should focus on "meeting customer needs and meeting modern enterprise management", with the help of electronics, information technology, and network technology, and strive to improve concrete mixing. The intelligent level of the station, wireless network control technology, remote fault detection and processing should be promoted, and the ultimate realization of "unmanned" concrete production plant.
(4) "Zero emission" should also be one of the important symbols of a "green" mixing station. After the national "environmental protection storm", the environmental protection performance of the mixing station has been improved. The emissions from mixing stations are mainly sewage and waste powder. Commercial mixing stations do better in this regard, but have they achieved "zero emissions"? Definitely not. Regarding the discharge of sewage, it can be said that "zero discharge" has been basically achieved. The mixing station uses recycled precipitated water for car washing, reducing the use of clean water. In addition, the mixing station uses part of the sewage (currently there are also technical problems), which basically solves the problem of sewage discharge. Problem; but the treatment of waste powder materials is still extensive. To put it bluntly, it means finding a place to dump it. Of course, the main responsible party for emissions is the research and utilization of concrete waste materials, which should be a subject of materials research. It is only clear here that "zero emission" is one of the important signs of a "green" mixing station.
(5) How to implement a "maintenance-free" mixing station? Judging from the current technical level, after visits and surveys in recent years, the failure rate of mixing plants as a first-line brand during use is still relatively low (the failure rate should mainly be concentrated in the installation and adjustment stage). Even if the user's maintenance is poor, In other words, there is no problem with the high reliability of the concrete mixing plant, but the maintenance problem is still quite prominent. With the increase in labor costs and the difficulty in recruiting workers, how to promote the "easy maintenance" of the concrete mixing plant until it is "maintenance-free" has become a matter of course. An urgent problem lies ahead. The maintenance of the mixing station at this stage mainly includes: first, cleaning of the binding materials, mainly including the main engine cover, belt conveyor return belt, dust removal pipeline, etc.; second, lubrication of the rotating parts; third, spreading the material at the overlap joint Cleaning up of leaked materials; fourth, maintenance of electrical systems (lack of professionals). Take the issue of adhesive materials. It can be said that the problem is the most prominent. If it is maintained well, it will require a lot of manpower. But there is no technical bottleneck in solving this kind of problem. There are two main ways to solve this contradiction using TRIZ theoretical analysis: one is to use materials that are not easy to bond, such as stainless steel plates, PE polymer composite plates, etc.; the other is to provide external forces, such as hoppers Or add a vibrator to the chute, etc. For example, the current 45-degree large-angle belt conveyor for aggregate transportation in the mixing station uses a chute with a vibrator and a return belt at the tail to solve a large material cleaning problem. If the materials are improved, the effect will be better. I won’t go into details here, but it is clear that the future of concrete mixing stations is an “unmanned” factory. These improvements must be made and done quickly, because these problems are not technical problems, but only application problems.
4 Conclusion
Green concrete mixing stations are inevitable for development. As a participant in industry development, we must strengthen our confidence, clarify our goals, and actively promote the technological progress of mixing stations. The market demand for concrete mixing stations is huge and it plays an irreplaceable position in the country's medium and long-term development plan, as can be seen from the high-speed rail plan recently released by the country. On August 13, 2020, China State Railway Group Co., Ltd. officially released the "Outline of the Advanced Railway Planning for a Strong Transportation Power in the New Era" and proposed that by 2035, the national railway network will reach about 200,000 kilometers, including about 70,000 kilometers of high-speed rail and 500,000 kilometers. Cities above the population are accessible by high-speed rail. As of the end of July 2020, the high-speed rail mileage was 36,000 kilometers, which is expected to be doubled within 15 years. The same is true for urban construction. With the development of large and medium-sized cities, "urban mixing stations" are also an important issue for the development of "green" mixing stations in the future. Therefore, concrete mixing stations will surely usher in a new period of development opportunities, and green concrete mixing stations will surely lead the development of the industry.